Industrial motor controllers
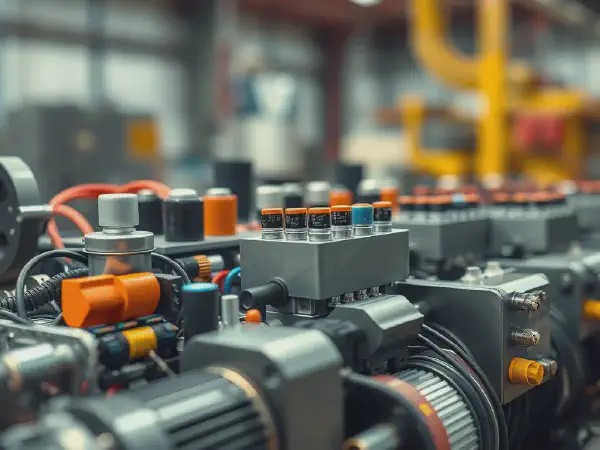
Industrial Motor Controllers
Introduction to Industrial Motor Controllers
Understanding Motor Controllers: Definition and Significance
Motor controllers are essential devices or sets of devices that regulate the start, stop, and speed of electric motors in various industrial applications. These controllers can be manually operated or programmed for automatic operation, offering functionalities like selecting rotational direction, adjusting speed, and protecting motors from overloads and electrical faults. By optimizing motor performance, controllers enhance energy efficiency, reduce operational costs, and ensure the smooth functioning of manufacturing processes and machinery.
Types of Motors in Industrial Applications
There are several types of motors utilized in industrial environments, each with unique characteristics suited for different applications:
-
AC Motor Controllers: Primarily used in controlling pumps, fans, and blowers, AC motor controllers modify power input to adjust frequency, thereby regulating output speed and torque.
-
DC Motor Controllers: These controllers govern speed and torque for applications such as machine tools and electric vehicles, offering simplicity and effectiveness.
-
Servo Motor Controllers: Known for precise control, servo motor controllers rely on position feedback mechanisms to maintain accuracy in positioning within closed control loops.
-
Stepper Motor Controllers: Commonly used for precise positioning and rotational control, stepper motor controllers are integral to motion control in manufacturing and construction sectors.
Types of Motor Controllers
AC Motor Controllers
AC motor controllers are designed to regulate the operation of AC motors by adjusting the voltage and frequency supplied to the motor. They primarily aim to control the speed and torque output, making them advantageous in applications that require precise speed control. AC controllers utilize power electronics to modulate input power, ensuring efficient motor function while adapting to varying operational demands. Examples of applications for AC motor controllers include pump systems, conveyor belts, and HVAC systems. The compact design of modern AC controllers, such as those from ABB, allows for easy integration into process industries while offering high durability and reliability across various environments.
DC Motor Controllers
DC motor controllers manage the speed and torque of DC motors by varying the input voltage to the motor. These controllers typically operate using techniques like pulse-width modulation (PWM), where the voltage is rapidly switched on and off to control the motor’s performance without wasting energy. DC motor controllers are widely used in industries such as manufacturing and automotive, where they power tools, electric vehicles, and packaging machinery. Notable advantages of DC motor controllers include simplicity in design, cost-effectiveness, and exceptional control over low-speed operations, making them suitable for applications requiring precise motion control.
Servo Motor Controllers
Servo motor controllers are integral in applications requiring high precision and reliability, such as robotics and aerospace. These controllers manage the position, speed, and torque of servo motors using feedback systems, ensuring that motors receive constant adjustments for optimal performance. Leveraging advanced control algorithms, servo controllers can achieve very tight control over motor output, making them ideal for tasks like robotic arm movements and automated machinery. The implementation of servo motor controllers helps enhance performance in applications that demand accuracy, such as CNC milling machines and drone flight control systems.
Stepper Motor Controllers
Stepper motor controllers facilitate the operation of stepper motors by sending specific pulses that dictate the number of steps the motor takes, thus achieving precise positioning. These controllers are fundamental in applications where accurate movement and positioning are crucial, such as in 3D printers, CNC mills, and various automation processes. Stepper motor controllers are known for their reliability and ability to provide high-torque performance at low speeds, making them indispensable in a wide range of manufacturing and assembly applications. Additionally, their capability to control multiple motors simultaneously makes them suitable for complex automation systems.
Industrial Motor Controllers Features | Benefits of Industrial Motor Controllers | Applications of Industrial Motor Controllers |
---|---|---|
Compact HF Electronic Starters | Easy and reliable motor starting | Process industry and factory automation |
Modular UMC Universal Motor Controllers | Optimized for various applications | Controlling speed of pumps, fans, and blowers |
High Durability | Long lifespan and reduced maintenance | Machine tools and electric vehicles |
Easy Installation | Reduced installation time and costs | Robotics and manufacturing processes |
Global Support | Assistance and resources worldwide | Various industries utilizing motor control |
Certificates for Worldwide Use | Compliance with international standards | Applications in regulated environments |
Key Features and Benefits of Industrial Motor Controllers
Compact Design and Durability
In industrial settings, motor controllers with a compact design are indispensable. They not only save valuable space but also enhance the ease of installation and integration into existing systems. The durability of these controllers is crucial, as they are often subjected to harsh environments, including temperature fluctuations, dust, and mechanical vibrations. Robust construction ensures they can withstand these conditions, minimizing downtime due to equipment failures. Motor controllers that boast compact and durable designs lead to increased reliability and longer operational lifespans, making them ideal for long-term industrial use.
User-Friendly Installation for Enhanced Operational Efficiency
Ease of installation plays a pivotal role in establishing operational efficiency within industrial settings. User-friendly motor controllers simplify the setup process, significantly reducing the time and effort required for installation. This is particularly advantageous in environments where speed is essential to maintain productivity. With fewer complications during installation, personnel can quickly integrate motor controllers into existing systems and get them operational faster. This seamless integration not only aids in minimizing training requirements for staff but also enhances overall workflow efficiency, allowing companies to focus on their core operations without delay.
Global Certifications and Support
Global certifications are essential for motor controllers, ensuring they meet international standards for safety and performance. This compliance is not only vital for legal regulations but also builds trust with customers who rely on these products in various global markets. Additionally, global support services play a critical role in the success of motor controller applications. With manufacturers providing comprehensive support—ranging from technical assistance to troubleshooting—companies can ensure optimal performance and rapid resolution of any issues that may arise. This combination of certifications and strong support networks reduces operational risks and enhances operational continuity across diverse geographies.
Tailored Solutions for Diverse Industrial Applications
One of the standout features of modern motor controllers is their ability to be optimized for a variety of industrial applications. Whether used in manufacturing, automation, or process control, these controllers offer flexibility that allows them to be tailored specifically to meet unique operational requirements. For instance, motor controllers can be programmed for different starting processes, control techniques, and operational parameters that match the specific characteristics of the motors they manage. This adaptability not only improves functionality but also contributes to energy savings and increases the efficiency of industrial processes, demonstrating the importance of having motor controllers designed for specific application needs.
Emerging Technologies in Motor Control
Enhancing Energy Efficiency with Variable Speed Drives
Variable speed drives (VSDs) play a crucial role in optimizing motor control systems, enhancing energy efficiency while significantly reducing operational costs. By adjusting the motor's speed and torque to match specific workload requirements, VSDs can decrease energy consumption by more than 30% when compared to traditional constant-speed motors. This capability not only results in lower energy bills but also extends the lifespan of the motor by minimizing wear and tear. Furthermore, the compact design of modern VSDs facilitates easy installation in various applications, thereby improving overall operational efficiency. Organizations that adopt VSD technology benefit from a dual advantage of cost savings and enhanced performance, making them a preferred choice for industries seeking to innovate and improve their processes.
Smart Technology Integration in Motor Controllers
The integration of smart technologies into motor controllers is revolutionizing the way these systems operate. With advancements in IoT (Internet of Things), motor controllers can now communicate in real-time with other devices, enabling predictive maintenance and remote monitoring. This connectivity allows operators to make data-driven decisions, optimizing motor performance and efficiency based on concrete operational data. For instance, smart controllers can analyze historical performance trends to adjust operational parameters dynamically, reducing energy waste. Moreover, this integration enhances safety features by providing alerts for potential system failures before they occur, ensuring lateral efficiency benefits in manufacturing and factory automation applications. The convergence of smart technologies with motor control signifies a fundamental shift in how industries manage their processes, promoting sustainability and operational excellence.
Anticipating Future Trends in Motor Controllers
Looking ahead, several trends are poised to shape the future of motor controller technology. One anticipated development is the enhanced use of artificial intelligence and machine learning in motor control systems. These technologies could enable automated tuning and fault detection, greatly increasing efficiency and decreasing downtime. Additionally, the ongoing push for greener solutions will likely lead to innovations focused on sustainable materials and energy-saving designs. The market is also expected to see a significant rise in the production of smart, connected devices, further aligning motor control capabilities with Industry 4.0 principles. As consumers and industries alike demand smarter, more efficient systems, the motor controller market will evolve rapidly, necessitating adaptive strategies to stay competitive.
Conclusion
Recap of Key Features and Advantages of Industrial Motor Controllers
Industrial motor controllers are essential in enhancing operational efficiency and ensuring precise control over motor functions. Key features highlighted in this article include:
- Compact Design: The small footprint facilitates easy integration into various applications.
- High Durability: Robust construction allows these controllers to withstand demanding industrial environments.
- Easy Installation: User-friendly designs simplify setup and reduce installation time.
- Application Optimization: Tailored solutions cater to specific process requirements, enhancing overall performance.
- Global Certifications: Compliance with international standards ensures compatibility across different regions.
- Comprehensive Support: Access to global technical support helps maintain operational continuity.
These attributes combine to improve productivity and reliability in industrial operations.
Insights on Future Trends in Innovation and Efficiency
Looking forward, the evolution of industrial motor control systems holds significant potential for enhancing industrial efficiency. As industries increasingly prioritize sustainability, the adoption of smart motor controllers equipped with advanced algorithms and IoT connectivity is likely to surge. These technologies will enable real-time monitoring and adjustments, leading to reduced energy consumption and optimized operational performance.
Moreover, the integration of machine learning and artificial intelligence could drive predictive maintenance, reducing downtime and prolonging equipment life. This not only enhances productivity but also minimizes costs associated with unplanned outages. As manufacturers invest in developing more sophisticated motor control solutions, we can expect significant advancements in efficiency and functionality, contributing to a more sustainable industrial landscape.
Frequently Asked Questions (FAQs)
Common Questions about Industrial Motor Controllers
What are the main functions of industrial motor controllers?
Industrial motor controllers are essential for managing the operation of electric motors. They control various aspects, including starting, stopping, speed adjustment, rotational direction, and torque regulation. Additionally, they provide protection to motors against overloads and electrical faults, thereby enhancing durability and efficiency.
What types of industrial motor controllers are available?
There are four primary types of industrial motor controllers:
-
AC Motor Controllers: Primarily used to control the speed of pumps, fans, and blowers by modifying the input power frequency.
-
DC Motor Controllers: Used for applications requiring precise speed and torque control, such as electric vehicles and machine tools.
-
Servo Motor Controllers: Offering precise control by using position feedback to maintain the desired motor position and speed.
-
Stepper Motor Controllers: Designed for accurate positioning and speed control in motion control applications.
How do motor controllers improve energy efficiency?
Motor controllers, especially variable-speed drives, enhance energy efficiency by adjusting motor speed to match load requirements. By replacing constant-speed motors with these advanced controllers, energy consumption can be reduced by over 30%, which can lead to substantial cost savings over time despite initial higher expenses.
Can motor controllers be used in harsh environments?
Yes, many modern motor controllers are designed to operate in challenging conditions, such as high temperatures, dust, and vibration. Using technology like Hall-effect sensors or variable reluctance sensors ensures reliable performance and accuracy in these environments, improving the overall durability and servicing of the motor systems.
How do I choose the right motor controller for my application?
Selecting the appropriate motor controller depends on several factors, including:
- The type of motor (AC, DC, servo, or stepper).
- The specific application requirements (speed, torque, environmental conditions).
- The desired level of control and feedback (closed-loop or open-loop systems).
Consulting with manufacturers or specialists can help in matching your needs with the right controller features.
What support is typically available for motor controllers?
Many leading brands, such as ABB and Siemens, offer global support services for their motor controllers. This includes installation assistance, technical help, and ongoing maintenance, ensuring users have the resources needed for reliable operation throughout the product’s lifecycle.
Are there certifications for industrial motor controllers?
Yes, motor controllers often come with various international certifications to ensure they meet safety and performance standards for worldwide use. These certifications can give users confidence in the reliability and safety of their motor control systems.
What advancements are being made in motor controller technology?
Innovations in motor controller technology include the integration of microprocessor-based systems for enhanced control, improved energy efficiency through advanced algorithms, and the development of high-speed ADCs for precise monitoring. These advancements enable greater flexibility and performance in industrial applications.